
Yellowfin Boosts DENSO Data Platform, Engages 14K Users
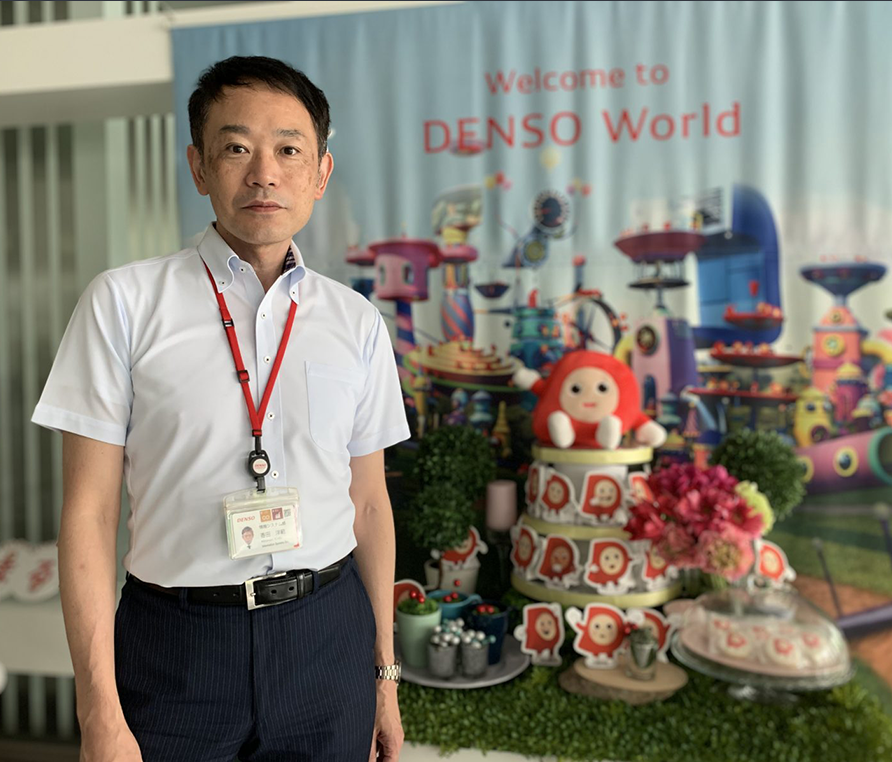
Background
DENSO is a world leading automotive parts manufacturer based in Aichi, Japan. Founded in 1949, the company focuses on developing core technologies in areas such as electrification, advanced safety, automatic driving, connectivity and non-vehicle business (factory automation/agriculture). Operating in 35 different countries and regions, it continues to provide technology that supports everyday well-being.
With an ageing core operation system and over 7,000 programs to account for, DENSO recognized the need for a better analytics solution to enable easier access to data. Yellowfin was identified as the best fit for helping the company with its pain-points and enhancing its core data systems.
DENSO leveraged its new solution for several objectives, resulting in increased usage of analytics, and reaching 14,000 maximum active users of Yellowfin. DENSO implemented Yellowfin in other areas of the business and continues to improve its operations efficiently and effectively.
I only recommend something I use myself to others – and more importantly, Yellowfin is so easy to use that even I can use it.
Hironori Koda, IT Technology Application Section Manager – DENSO CORPORATION
Challenge
DENSO’s core workflow centered on its information technology division preparing and delivering all data for its end-users. Each user department then utilized this prepared information for their daily operations.
In 2014, the company identified its core operation system as too complicated to maintain after more than 30 years running. This was mainly due to an inconsistent code architecture and an only once-per day data refreshment cycle. Eventually, no one in the business had a whole picture of the system since most of the original developers had retired, introducing a significant challenge. But when the company decided to replace the system due to its complex architecture, it needed to ask its users to change their ways of operations.
The company initially started to move its product management system to Yellowfin since this was the most complicated system which had a lot of trouble utilizing data. At that time, there were around 7,600 programs that needed to be migrated, and no one knew which needed to be moved into the new platform, so it asked its users to check each program and move it into Yellowfin: “Listing all those programs was an easy task, but we could not judge which one was needed for our users’ operations, so asked them to check each of them and move it into Yellowfin,” said Hironori Koda, IT Technology Application Section Manager at DENSO.
This highly manual task required extra effort outside of their daily operations, and it could not be completed even after two years. Due to the long migration time, the replacement project itself was eventually canceled, as DENSO experienced difficulties in motivating staff to migrate.
However, a number of users had already moved their program, accelerating DENSO’s need to find another way to increase user adoption of Yellowfin.
Solution
DENSO decided to leverage Yellowfin for different objectives. At that time, they still had a lot of tasks, such as downloading data from its host server, calculating data using Excel, and sending reports attached to emails. Management helped users recognize, with Yellowfin, they could eliminate time-consuming manual those efforts and improve efficiency overall.
To start with, DENSO conducted a survey to understand Yellowfin usage among the 1,700 initial users. It turned out about 60% didn’t really know what Yellowfin was; however, they did show interest in learning about its features in more depth, which led the company to hold regular training sessions to better educate its staff who had not used Yellowfin before during the initial migration.
“From the survey results, more than half of the users answered that they wanted to learn its features in more depth if there was a chance, and I felt there was a great opportunity to expand the usage of Yellowfin,” said Koda. The more the company held the training sessions, the more its people started to use Yellowfin as they realized they had been using it inefficiently.
After Yellowfin usage was dramatically increased, DENSO decided to hold consulting sessions to address issues the users faced during their daily operations. With huge help from our partner NTT-TX, the company fulfilled many requests from the users, resulting in increased usage overall with the maximum number of active users reaching 14,000 and the average number around 6,000 – about three times more than the initial user base.
After holding the training and consulting sessions, staff started to share what they had learnt with other departments, factories and regions. As a result, Yellowfin Japan started to get more demo requests from other parts of DENSO where Yellowfin had not yet been implemented.
Benefits and Future
As a manufacturer, inventory management is important to produce products. Before, DENSO could not manage its overseas locations as effectively as they targeted, as it took significant time to get data and create reports for further analysis. After implementing Yellowfin, the company connected data directly from overseas, so that they now can create reports far more easily, which opens up deeper analysis across its entire user base.
Previously, if something unexpected or urgent happened in the procurement workflow, DENSO staff needed to deal with the situation by manually checking data to find a site with extra capacity for production. With Yellowfin now widely in place, staff – including partners and vendors – are able to visualize their data and take necessary action far more quickly.
DENSO now runs annual surveys for the entire staff by department to determine if there are any blockers at their workplace or how engaged they feel while completing daily tasks. There are more than 200 departments, and it previously took about 2 months to manually collect all the information and create results as they had used Excel for the workflow. After creating a dashboard in Yellowfin, they now enable users to get results instantly after the survey is conducted, and utilize that information to improve the efficiency of their operations, which they have never been able to accomplish previously. There is a lot of sensitive information included in the survey results, and Yellowfin’s flexible security and role-based access settings work well for them to deliver only related information to authorized users.
DENSO are also using Yellowfin to great effect for its logistics management. They need hundreds of distribution trucks to deliver products, and controlling the volume with each truck is crucial since it affects the cost. Previously, they were calculating and planning the volume monthly and manually, but with Yellowfin, it is now possible for its users to follow the daily distribution more easily, and manage the products cost effectively. “I only recommend something I use myself to others, and more importantly, Yellowfin is so easy to use that even I can use it,” concludes Koda.
DENSO still has a huge amount of data outside of Yellowfin and are planning to create an enterprise data catalog for its users, so they can analyze whatever is necessary. They also aim to connect with all its office locations and factories to continue to better utilize data throughout the enterprise.
DENSO, NTT-TX & Yellowfin Japan teams smile for the (Zoom) camera!
See for yourself
Let us show you the best analytics product on the market with the only analytics platform that combines action based dashboards, automated business monitoring and data storytelling capability.
Get a Demo